Using Two Different Laser Cladding Materials Increases Ductility of Joint and Avoids Formation of Cracks
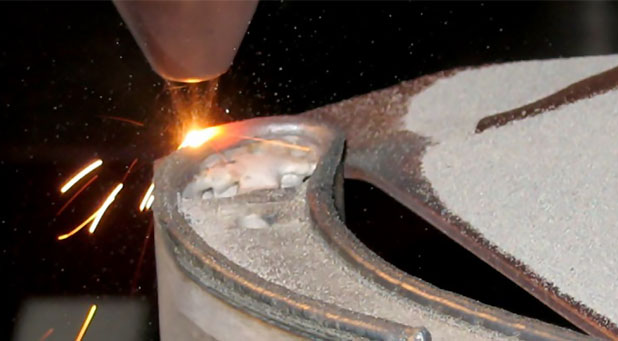
Laser cladding refers to a surface modification technique widely used in industrial applications such as rapid manufacturing, parts repair, surface coating, and innovative alloy development. It involves the feeding of a stream of metallic powder or wire into a melt pool that is generated by a laser beam as it scans across the target. Laser cladding can be used to increase corrosion resistance, wear resistance or impact performance of metallic components, using a method of applying a fully dense, metallurgically bonded and virtually pure coating. Laser cladding materials with different lasers have been used: high power diode laser (848 nm), Nd:Yag laser (1064 nm), CO2 laser (10.64 µm), and excimer laser (248 nm). It is quite different from traditional welding or fusion bonding as a means to permanently bind the metals together by means of high-energy laser beams. Instead, it is usually achieved by injecting two metallic materials through a cryogenic chamber and then pressing or...